Digital Twins Will Aid Digital Transformation In 2020
I wrote recently on this blog about the use of SAP to create Digital Twins, a digital representation of a real system so it can be more easily monitored and controlled. As I mentioned earlier, this has been a common practice in aviation for several years. Engine manufacturers will always maintain a digital version of every engine they sell and ensure that the digital version is updated in real-time using sensors on the real engine.
In aviation the advantage of doing this is obvious – it allows for more efficient maintenance and safety procedures when the digital engine allows engineers to monitor real engines remotely. But I believe that the launch of SAP’s Leonardo system last year will really start accelerating the use of Digital Twins as a common business strategy.
It is a combination of technologies and strategies that are creating this possibility, but the three important ones are:
1. The Internet of Things (IoT); as the real world fills with sensors and connectivity as standard for almost every electronic device we will reach a point where systems such as a Digital Twin are essential just to stay on top of what is connected and what information it is reporting. In the home, this may only be devices such as a Kindle, iPad, Echo, phone, lightbulbs, or heating thermostat, but in the industrial environment it can easily be more complex and difficult to control.
2. Artificial Intelligence (AI); with so much data being created constantly by sensors we will need to apply AI principles to the data just to make sense of it all. For example, if your home thermostat detects patterns in the way that you prefer your home to be heated then it should be able to anticipate what you want before you change the settings.
3. Machine Learning (ML); the ability to look at every action and outcome by every sensor inside a network will allow the system to learn about the ideal outcomes and then to suggest recommendations in future based on earlier learning.
It is really the IoT that is at the heart of this development. Imagine the complexity of a modern industrial facility – a large brewery or car factory for example. Across the entire property will be doors, windows, pumps, and various robots that all need to be coordinated. Most companies with these facilities will already have some sort of control mechanism, but the Digital Twin makes an assumption that every component (pump, door, assembly-line robot) has in-built sensors. By taking a feed from all of these sensors we can build a complete virtual mirror of the plant.
The IoT facilitates this by ensuring that the real-time sensor data is available, then the AI system goes to work on spotting potential problems or just process flows that are unusual and alerting workers to places they need to check.
I have seen this type of system deployed for an office management system where every light, heater, door, and window is modelled in the system. I believe that we will see the Digital Twin concept growing much faster as companies find that they can create enormous efficiencies by improving what they do and spotting problems before they happen.
As Forbes magazine recently suggested, it will soon be impossible to plan any kind of digital transformation for your business without creating a digital twin first. The processes will be simply too complex for any one manager to understand from start to end. Not only do you need to map out all the existing components, you need to apply AI to oversee how the entire system is working.
Without these deep insights into the way your business functions at present any transformation plans will be impossible. Digital Twins are not just for those obsessed with being able to manage their existing IoT infrastructure, they are becoming an essential tool for managers who want to see how the future of their business might look.
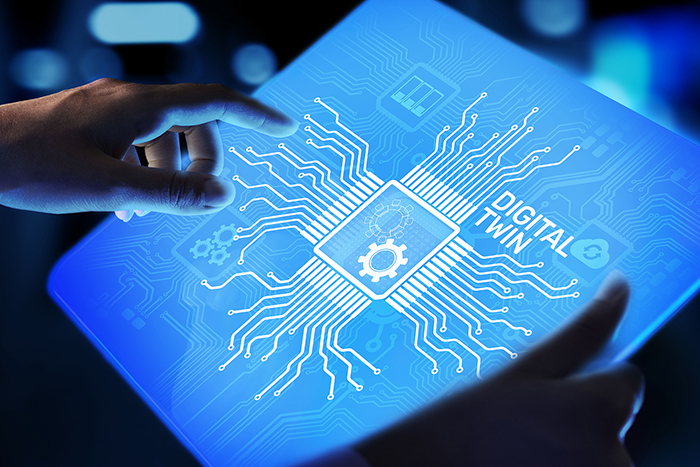